Neljä viikkoa on 28 vuorokautta, mikä tarkoittaa 672 tuntia, eli 40320 minuuttia. Tästä kokonaisajasta sohvan tekemisen työvaiheisiin on yhteensä mennyt 57 minuuttia. Mitä tilaukselleni on tapahtunut noiden neljän viikon aikana, kun olen odottanut tuotetta? Asiakkaalle arvoa tuottavan ajan (VA) osuus on vain 57 minuuttia ja loppu 40263 minuuttia on Ei arvoa tuottavaa (NVA) aikaa.
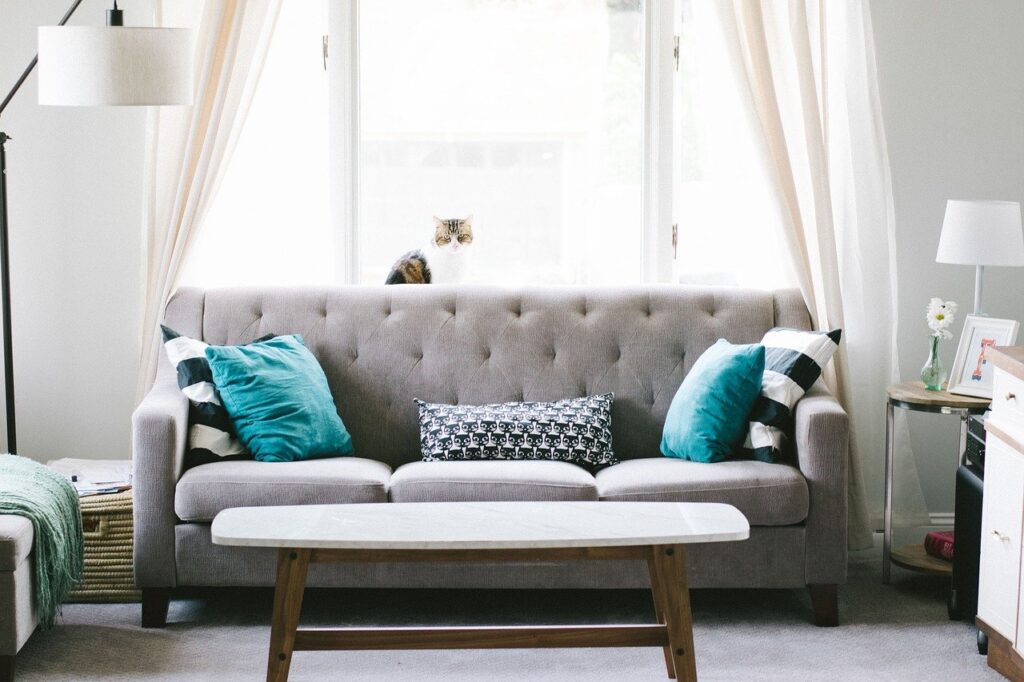
Huonekalukauppa on vain yksi esimerkki. Sama kuvio toistuu hammaslääkärissä. Tilaan hammaslääkäristä ajan ja saan sen viiden viikon kuluttua. Tuosta viiden viikon kokonaisläpimenoajasta olen tuolissa noin kymmenen minuuttia. Sama koskee markettien jonoja tai puhelinoperaattoreiden palvelunumeroa. Asioimiseen menee aikaa muutama minuutti, mutta palvelua voit joutua odottamaan useita tunteja.
Toki sohvatilaukselleni on tapahtunut paljonkin erialaisia asioita prosessin varrella: Se on kirjattu sisään, siitä on tehty tilaukset raaka-aineen toimittajille ja alihankkijoille. Materiaalin toimittaja on tehnyt tilauksen kangastehtaalle. Puuosat ja rungot on tilattu alihankkijalta. Materiaaleja ja osia on odotettu ja niiden toimitusaikaa on selvitetty useamman henkilön toimesta. Huonekalutehtaassa tilaukseni on laitettu tuotannon kuormituslistalle odottamaan omaa vuoroaan. Tilaukseni odottaa, koska tuotantoprosessissa tehdään edelleen suuria eriä kalusteita koneilla, jotka eivät toimi suunnitellulla nopeudella ja saanto on alle 80%. Pitkät aseteajat ovat ilmeisesti syynä suuriin erätuotantoihin. Valmistusvaiheiden jälkeen sohvani odottaa lähettämön lastaussillalla niin kauan, että suuntakuorma saadaan täyteen. (Tyhjällä autolla ei kannata terminaalien välejä ajella.) Terminaalista sohvani sitten kuljetetaan huonekaluliikkeen noutovarastoon, josta sen voin sitten itse noutaa tai sopia kuljetusliikkeen kanssa kotiin kuljettamisesta.
Kun sohvan jälkilaskelma myyntiorganisaatiossa vihdoin valmistuu, niin harvoin siinä kohtaa kukaan huomioi kokonaisläpimenoaikaa tai saati sitten arvoa tuottavan ja tuottamattoman ajan suhdetta keskenään. Yleensä katsotaan vain ne etukäteen suunnitellut tuotantoajat, niiden toteutuminen ja myyntikatteet. Ei ymmärretä, että jalostavat tuotanto-operaatiot (yhteensä 57 min) ovat liikevaihtoa ja loppuaika (40263 min) on mitä suurimassa määrin kustannus. Suurin osa tuon neljän viikon läpimenoajasta on asioiden selvittämistä, etsimistä, odottamista ja kaikenlaista hukkaa. (Ei arvoa tuottavaa (NVA) aikaa.) Eli ihan normaali, jokapäiväinen kuvio useassa tuotantolaitoksessa.
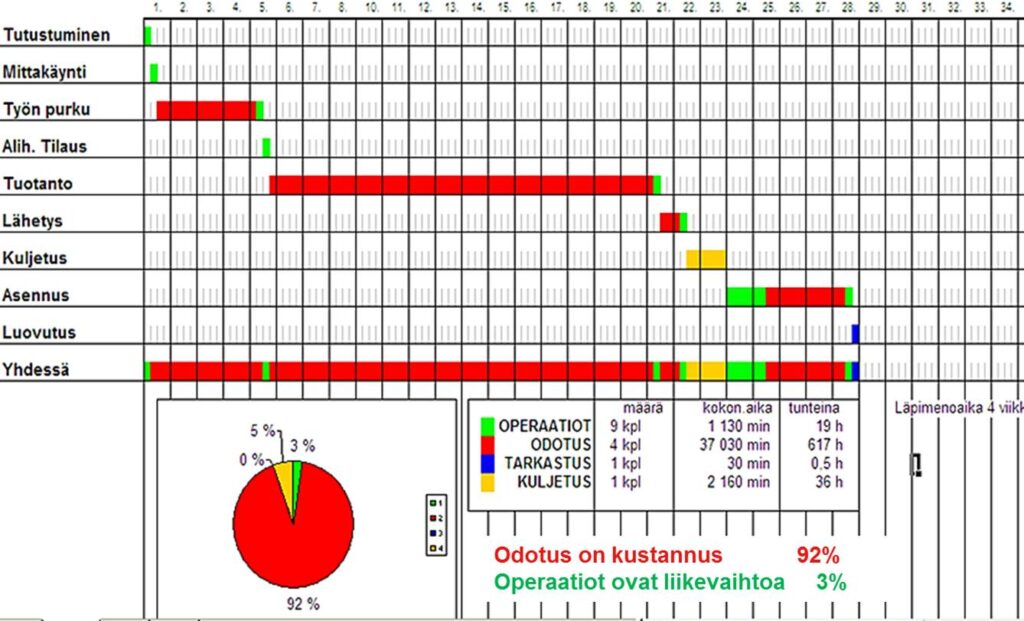
Onko sinun tuotannossasi tiedostamattomia jonoja, odotusaikoja, tuotantokatkoja, nopeuden menetyksiä tai pullonkauloja? Pystyttäisiinkö olemassa olevaa tuotantokapasiteettia käyttämään paremmin hyödyksi? Tiedätkö sinä mistä yrityksenne kustannukset syntyvät?
Miten tätä yleistä ongelmaa voitaisiin korjata? Voisiko näistä seuraavista menetelmistä olla apua?
Tutustu Leaniin
Mitä Lean on? Se on asiakaslähtöinen prosessijohtamisen malli, joka perustuu virtauksen (exit rate) maksimointiin ja hukan (menetetty aika) poistamiseen. Se on toiminta ja ajattelutapa, jossa virtausta ja jalostusarvon osuutta maksimoidaan poistamalla hukkaa. Läpimenoajan lyhentäminen (nopeuden kasvattamisen) on yksi keskeisistä päätavoitteista. Jos läpimenoaika ei lyhene, niin todennäköisesti taloudellista parannusta ei saavuteta. Lean -toimitusketjun tavoite on lisätä asiakkaalle arvoa tuottavan ajan osuutta prosessissa. Parannustoiminta kohdistetaan ja priorisoidaan tunnistettuun arvovirtaan. Priorisoimalla parantaminen lisäarvoa tuottaviin toimintoihin ja poistamalla hukkaa kuljetaan kohti ideaalista arvovirtaa, jonka tahtiaika sykkii läpi koko prosessin samassa tahdissa asiakastarpeiden mukaan.
Luokittele ja poista hukkaa (Waste)
Hukka, Waste, Muda on mitä tahansa, joka lisää kustannuksia ja odotusaikaa antamatta lisäarvoa asiakkaalle. On olemassa kolme hukan luokkaa: Muda, joka jakautuu 7 hukkaan. Mura on epätasapaino ja Muri, on vaihtelu, joka generoi kaikki muut hukan muodot. Yleisesti hyvissäkin yrityksissä asiakkaalle arvoa tuottavan ajan osuus on alle viisi prosenttia ja loppu yhdeksänkymmentäviisi prosenttia on hukkaa. Se on menetettyä aikaa ja resurssia, joka ei nosta tuotteen tai palvelun jalostusarvoa prosessissa. Japanilaiset ymmärsivät nimetä ja luokitella hukan, jonka jälkeen yrityksen koko organisaation tehtävänä oli ponnistella voimakkaasti hukan poistamiseksi. Prosesseissa hukan osuus on usein yli 95 %. Poistamalla hukkaa, jalostusarvoa sisältävän ajan osuus kasvaa. Tyypillisesti hukka tunnistetaan ja luokitellaan seitsemään tai kahdeksaan hukkaan: Ylituotanto, odotus, kuljetus, yliprosessointi, varastot, liike, viat, ja käyttämättömät taidot.
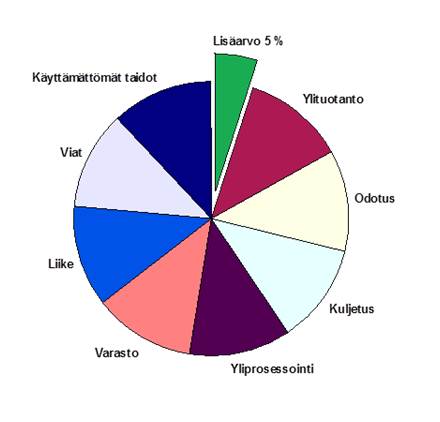
Lyhennä läpimenoaikaa (Lead time)
Läpimenoajalla tarkoitetaan tilaus-toimitusprosessin kokonaisläpimenoaikaa, jota lyhentämällä saavutetaan tuottavampi ja virtaavampi prosessi. Leanin tavoitteena on maksimoida asiakastyytyväisyys. Perustana tälle on asiakaskysynnän täydellinen ymmärtäminen. Tämä ei siis tarkoita ainoastaan laadullisia asioita, vaan kokonaisvaltaista prosessin ymmärtämistä toimitusmääristä, taajuudesta ja laatuvaatimuksista. Niinpä Leanissa keskeisin tekijä onkin aika. Virtausta parannetaan läpimenoaikaa (Lead time) lyhentämällä. No mitä se virtaus on? Virtauksella tarkoitetaan prosessissa olevan tuotteen tai palvelun liikettä ylävirrasta alavirtaan, eli raaka-aineesta kohti lopputulosta. Pitkä läpimenoaika on seurausta erilaisista hukan muodoista, ja perimmiltään vaihtelusta. Vaihtelu aiheuttaa virheitä, vikoja ja hukkaa. Tämän vuoksi asiat eivät ole ratkaistavissa suoraan Lean -työkalulla, vaan Lean -työkalujen rooli on nostaa ongelmat esiin. Tarvitaan siis ongelmanratkaisua, jonka avulla selvitetään syy hukkiin ja tehdään onnistuneita ja pysyviä muutoksia prosessiin. Poistamalla prosessista hukkaa ja kehittämällä prosessia suoraviivaisemmaksi, virtaus luonnollisesti kasvaa.
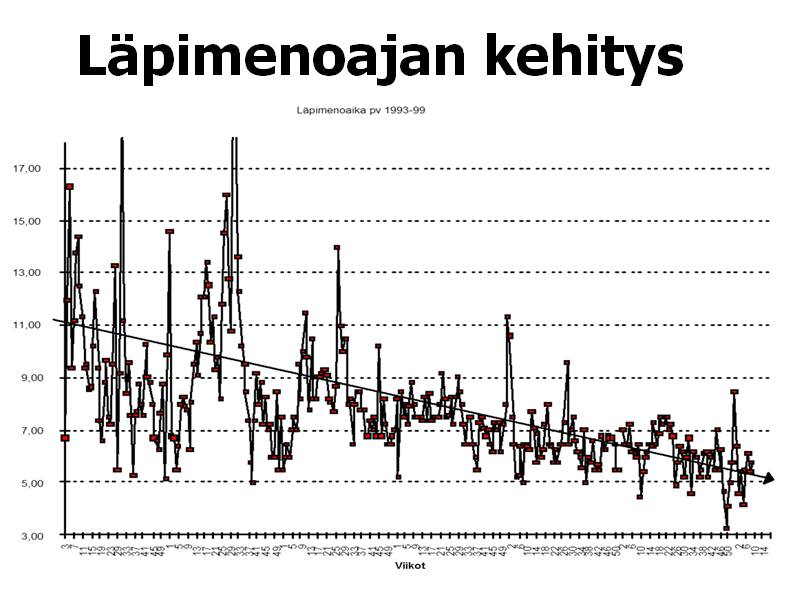
Tee arvovirtakuvaus (VSM, Value Stream Mapping) ongelmien tunnistamiseksi
Leanin yhtenä menetelmänä käytetään arvovirtakuvausta (VSM, Value Stream Mapping) virtauksen esteen tunnistamiseen ja priorisointiin. Oikeiden ongelmien tunnistaminen ja niiden ratkaiseminen on keskeistä tehokkuuden eli nopeuden nostamisessa ja läpimenoajan lyhentämisessä. Arvovirtakuvauksen (VSM) avulla ymmärretään, kuinka materiaalit ja informaatio virtaavat tilaus-toimitusprosessissa. Arvovirtaus on kokonaisjaksoaika (tai läpimenoaika), joka kuluu, kun asiakas esittää tilauksensa ja saa sen käyttöönsä. Tämä aika pyritään saamaan niin lyhyeksi kuin mahdollista. Kuvauksen avulla paikallistetaan pullonkaulat ja keskeneräisentyön varastot (WIP). VSM tuo yhteisen kielen- ja näkemyksen organisaatioon ja osoittaa, kuinka toiminnot todella toimivat päivittäin. VSM kuvaa asiakkaat, tavarantoimittajat, informaatiovirrat, materiaalivirrat ja prosessin yhdeksi arvovirtakuvaksi.
Käytä TOC-teoriaa (Theory of Constraints) prosessin ohjaukseen
TOC-teoriaa (Theory of Constraints) voidaan kutsua esteiden teoriaksi. Usein arkikielessä siitä käytetään termiä pullonkaula tai kapeikkoajattelu. Se perustuu ajatukseen, että jokaisessa järjestelmässä tai systeemissä on aina yksi este tai jokin rajoittava tekijä kerrallaan. Este tai pullonkaula rajoittaa siis tavoitteeseen pääsyä. TOC perustuu E. Goldrattin kehittämiin ajatuksiin, jotka hän julkaisi kirjassaan The Goal (1984). Näitä teorioita hän on jatkokehittänyt myöhemmin kirjoittamissaan kirjoissa. Teorian avulla pyritään tuottavuuden parantamiseen tunnistamalla ensin tavoitteeseen pääsemisen este, pullonkaula tai kapeikko, ja sen jälkeen hallitsemalla ja ohjaamalla tuotantoprosessia tästä pisteestä. Käytännössä tämä tarkoittaa sitä, että tunnistettua kapeikkoa pyritään laajentamaan paremman virtauksen saavuttamiseksi. Kapeikkoa voidaan käyttää myös tuotantoprosessin ohjauspisteenä. Kun tuotantoa ohjataan tästä pisteestä, niin tuotannon aikataulutus tehdään tämän pisteen kapasiteetin mukaan. On tärkeää, että tässä pisteessä on koko ajan työtä ja sen jatkuva toimiminen varmistetaan pienellä tuotannon varastolla (WIP). Tämä pullonkaula määrää tuotannon kokonaisläpimenoajan. Pullonkaulassa säästetty tunti on koko prosessissa säästetty tunti.
Mittaamalla OEE (KNL, Käytettävyys, Nopeus, Laatu), saat tuotantolinjan todellisen tehon
Vaikka tuotanto näyttää sujuvan hyvin, prosessinosissa voi olla huomattaviakin menetyksiä käytettävyyden, nopeuden tai laadun suhteen. Tehtaan tuotantolinja saavuttaa harvoin täyttä sadan prosentin kapasiteettiaan. KNL lyhenne pohjautuu alun perin englantilaiseen termiin OEE (Overall Equipment Effectiveness) , joka on myös käytössä virallisen, suomalaisen rinnalla. KNL -laskennan perustana on kertoa kolme osatekijää (käytettävyys x nopeus x laatu) keskenään, jolloin nähdään, millä osuudella teoreettisesta kokonaistehosta tuotantolinja käy. Jos käytettävyys, nopeus ja laatu ovat kukin kohtuullisen hyviltä vaikuttavat 85 prosenttia, (0,85 x 0,85 x 0,85) x 100 niin kokonaistehokkuus onkin vain 61,4 prosenttia.
KNL paljastaa aikamenetyksiä ja vääriä toimintatapoja, ja sen käyttöönotto on askel toimintakulttuurin muutokseen. Asian ymmärtäminen kokonaisuutena on helpompaa, kun eri toimintojen vuorovaikutukset näkyvät numeroina. Kustannukset ja aikamenetykset syntyvät koneiden seisokista: kone ei käy, vaikka sillä pitäisi ajaa tuotantoa. Kustannuksia ja aikamenetyksiä syntyy myös tuotteiden huonosta laadusta: Tuotteita ei saada tehtyä ensimmäisellä kerralla oikein, vaan ne joudutaan korjaamaan tai valmistamaan uudestaan. Tiedostamattomia aikamenetyksiä ja kustannuksia syntyy alentuneesta tuotantonopeudesta: kone käy, mutta esimerkiksi huollon puutteesta johtuen se ei valmista tuotteita koneelle asetetulla tavoitenopeudella.
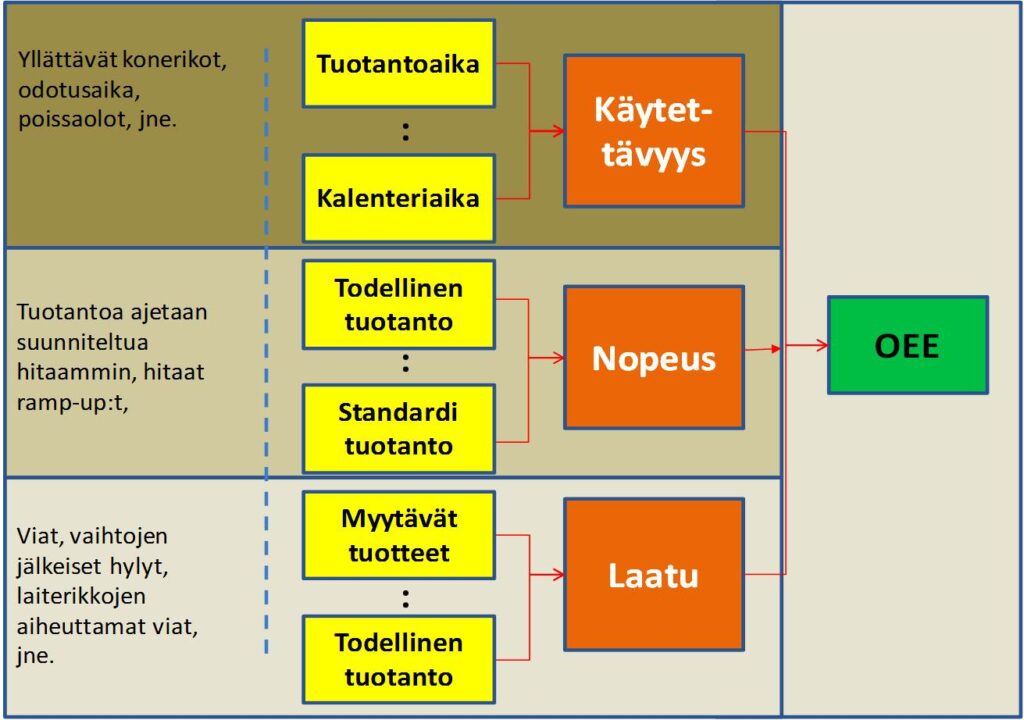
Kiinnostu, opiskele ja innostu
Tässä vielä lisäksi muutama menetelmä tai työkalu, johon kannattaa tutustua syvemminkin. On olemassa useita erilaisia Lean –menetelmiä ja työkaluja, joilla prosessien välistä vaihtelua ja hukkaa voidaan pienentää ja arvovirtaa tehostaa. Esimerkiksi: Tahtiaika, 1×1 virtaus, Heijunka, Poka-Yoke, SMED, Kanban -imuohjaus, TPM (Total Productive Maintenance), 5S -menetelmä, Laatutaulut, SPC jne.
On tärkeää ymmärtää, että Lean on ensi sijassa johtamista ja kulttuurin muutos, jossa johtajat toimivat organisaatiossa Lean -hankkeiden ja projektien sponsoreina. He johtavat, tukevat, suojelevat, edistävät ja levittävät organisaatiossa Lean -toimintaa. Työkalujen merkitys korostuu joskus liikaa ja niiden rooli ymmärretään usein väärin. Ensin pitää ajatella ja ymmärtää mitä halutaan, pitää olla tavoite. Yleinen väärinkäsitys on, että Leaniin liitetyt työkalut itsessään ratkaisisivat ongelmat. Työkalujen tarkoituksena on kaivaa prosessista ongelmat esiin. Ihmisten tehtävänä on ratkoa työkalujen ja konseptien avulla esiin tulleet ongelmat. Ongelmat ovat jalokiviä! Työntekijöiden tehtävänä on nostaa ongelmat esiin työkalujen avulla ja esimiehillä pitää olla riittävä tietotaito ongelmien ratkaisemiseksi. Jos työkalujen ja konseptien roolia ei ymmärretä oikein, ei Lean-projekteilla päästä haluttuihin tuloksiin.
Tilaa uutiskirje
Liity postituslistalle ja saat uusimmat artikkelit suoraan sähköpostiisi.
Tämä lomake on suojattu Google reCAPTCHA:lla. Lue tietosuojaseloste ja käyttöehdot.
Liittymällä postituslistalle hyväksyt Quality Knowhow Karjalainen Oy:n tietosuojaselosteen ja Quality Knowhow Karjalainen Oy voi lähettää sinulle ajankohtaisia artikkeleita, videoita sekä tietoa ja tarjouksia kursseista, kirjoista sekä ohjelmistoista.
Tämä lomake on suojattu Google reCAPTCHA:lla. Lue tietosuojaseloste ja käyttöehdot.