Lean ja hukka. Onko hukan tunnistaminen päämäärä vai keino? Parantaako hukan tai ei arvoa lisäävän ajan poistaminen aina tuottoa? Mitä hukka on ja mitä se kertoo toimintaolosuhteista?
Lean on prosessijohtamisen filosofia, joka keskittyy parantamaan asiakkaan kokemaa arvoa kasvattamalla prosessin keskimääräistä virtausta, läpimenoa (throughput), poistamalla arvon muodostusta tai läpimenoa estävää hukkaa (waste)/1/. Arvon lisääminen ja läpimenon kasvattaminen ovat tavoite ja hukka on keino. Tavoite ja keino voivat mennä jossain yhteydessä sekaisin. Lean on siis strategia, kuinka saavutetaan enemmän parempia tuotteita tai palveluita samoilla resursseilla.
Arvolla tarkoitetaan ominaispiirrettä (asiaa tai tekijää), josta asiakas on valmis maksamaan enemmän kuin sen tuottaminen maksaa. Tästä erosta muodostuu yritykselle kate. Jos arvon tuottaminen tulee kalliimmaksi kuin siitä maksetaan, tulee liiketoiminnasta kannattamatonta. Tästä voidaan johtaa viisi keinoa parantaa kannattavuutta:
- enemmän arvoa (hintaa) samoilla panoksilla (samalla kustannuksella)
- sama arvo pienemmillä panoksilla
- enemmän arvoa pienemmillä panoksilla
- paljon enemmän arvoa hieman kasvavilla panoksilla
- vähemmän arvoa paljon vähemmillä panoksilla
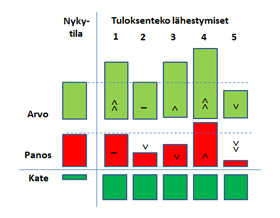
Tuotannossa arvo muodostuu toiminnossa, joka voi olla työasema, kone, laite tai työpiste, jossa myytävä tuote muodostuu. Palvelussa tämä tarkoittaa työsuoritusta, joka tapahtuu asiakkaan läsnä ollessa (Front Office) tai palvelutapahtuman taustalla (Back Office). Arvon tuottaminen, se minkä asiakas kokee ja saa, vaatii aina aikaa. Tätä aikaa kutsutaan arvoa lisääväksi ajaksi/2/ tai raa’aksi prosessiajaksi (Raw Process Time)/3/. Koska käytettävissä oleva aika on aina rajallinen ja arvoa lisäävä aika aina vaihtelee erilaisista syistä johtuen, saadaan tuotteita tai palveluja eri tarkasteluvälillä eri määrä. Mitä lyhyempi on raaka prosessiaika sitä enemmän valmistuu tuotteita per tarkasteluväli (katso kuva 2).
Läpimeno tarkoittaa pitkän aikavälin keskimääristä valmistumisnopeutta/3/. Nopeutta mitataan tyypillisesti kpl tai tapahtumaa per aikayksikkö. Esimerkkinä läpimenosta voisi olla valmistuneiden tuotteiden määrä per 8 tuntia tai tuotettujen palveluiden lukumäärä per 8 tuntia. Läpimenon kasvaessa samoilla resursseilla voidaan kannattavuutta hakea edellä esitetyn viiden vaihtoehdon avulla (kuva 1).

Hukka-aika
Leania käsittelevissä kirjoissa Lean-ajatusta usein perustellaan seuraavanlaisesti:
Kokonaisjaksoaika = Arvoa lisäävä aika + Ei arvoa lisäävä aika/2,3/
Total Cycle Time = Value Added Time + Non Value Added Time
Kaava kuvaa, mistä kokonaisjaksoaika muodostuu, mutta se ei kerro koko totuutta. Kaavasta saa helposti sellaisen kuvan, että ei arvoa lisäävän ajan poistaminen johtaa aina parempaan. Näin ei todellisuudessa tapahdu kuitenkaan usein. Kaavassa on ainakin seuraavat kaksi ongelmaa:
- oletetaan (ja usein ihmisetkin), että ei arvoa lisäävän ajan poistuminen siirtyy automaattisesti arvoa lisääväksi ajaksi ja
- kaava ei ohjaa siihen, mitä pitäisi tehdä ei arvoa lisäävän ajan poistamiseksi.
Väittämä on sama kuin laatuohjeeksi sanoisi, tee vain hyviä tuotteita, koska virheelliset tuotteet + virheettömät tuotteet ovat kokonaistuotantomäärä. Keskeinen kysymys on: kuinka tuotetaan hyviä tuotteita ja mihin parannus tulee toteuttaa.
Tuotanto, onpa kysymyksessä tuote- tai palveluympäristö, on systeemi. Systeemillä tarkoitetaan kokonaisuuden joukkoa, jossa yksittäisten osien välillä on riippuvuussuhteet. Tämä tarkoittaa käytännössä, sitä, kun muutos tehdään johonkin se vaikuttaa toisiin systeemin osiin. Vaikutus voi olla joko positiivinen tai negatiivinen. Lean -projektien tai käyttöönottojen tulokset eivät puhu onnistumisen puolesta. Onnistumiset ovat muutaman prosentin luokkaa. Onnistumisella tarkoitetaan muutosta parempaan kovissa mittareissa, onpa nämä mittarit talous- tai läpimenoa käsitteleviä mittareita.
Esimerkki:
Kuvassa 3 on esitetty yksinkertainen prosessi. Tämä voi olla joko tuotanto- tai palveluprosessi. Kuvasta huomataan, että vaiheen yksi ja kaksi edessä sekä prosessin loppupäässä on keskeneräistä työtä. Kun tätä työmäärää arvioidaan suhteessa kysyntään havaitaan, että prosessissa on yhdeksäntoista päivän kysyntää vastaava työmäärä (Littlen lakia käsitellään artikkelissa: Onko kaikki erilaista vai ei?). Toinen huomioitava asia on, että vaihe yksi on prosessin pullonkaula.
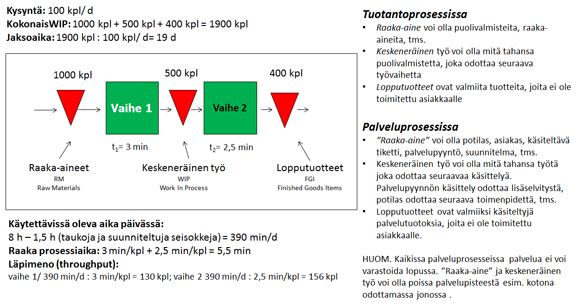
Odotusaika prosessivaiheiden välissä – varasto- ja odotushukka
Yrityksessä ja organisaatioissa kertyneille varastoille ja jonoille on olemassa jokin syy. Usein ne ovat kertyneet sinne suojaamaan toimintaa erinäisiltä vaihtelun lähteiltä (vaihteluun suojautumisen laki). Vaihtelun lähteet voivat olla epästabiilisuudesta tai alhaisesta suorituskyvystä johtuvia lähteitä /4,5/ (Mitä pitäisi ymmärtää datasta – tilastoista? OSA II ja osa III). Jos varastot ovat kertyneet tai asetettu aiemmin tarpeeseen, niiden tasojen laskeminen vaikuttaa virtaukseen ja tätä myötä arvon tuottamiseen. Varasto ja läpimeno ovat toisin sanoin riippuvuussuhteessa. Tässä tapauksessa arvoa lisäämättömän ajan poistaminen ei kasvata arvoa eikä lisää läpimenoa vaan vähentää. Tämä ilmiö johtuu taustalla olevien tekijöiden keskinäisvaikutuksesta. Varastotasojen tiputtaminen vaatii usein toimintaolosuhteiden ymmärtämistä ja onnistuneita toimenpiteitä toimintaolosuhteen muuttamiseksi. Perus lainalaisuuksien ja vaihtelun tunteminen auttaa ymmärtämään keskinäisvaikutuksia.
Jos taas varastot ovat kertyneet prosessiin turhaan, niin silloin ne kannattaa poistaa, mutta edelleenkään se ei tuo lisää läpimenoa. Varastotasojen vähentäminen voi tuoda joitain muita hyötyjä (arvoa yritykselle, mutta ei suoraan asiakkaalle). Tämä edellyttää, että ylimääräinen varasto ja materiaalin odotusaika on liiketoiminnan kannalta kriittinen tekijä. Jaksoajan lyhentyessä ennusteen tarve lyhenee ja näin ennustevirhe pienenee ja sen vaikutus ei aiheuta lisää vaihtelua. Toisaalta vapautuu tilaa esim. uudelle työlle, varastojen hallittavuus paranee ja vaihto-omaisuuden arvo pienenee. Nämä hyödyt ovat kuitenkin usein huomattavasti taloudellisilta vaikutuksiltaan vaatimattomampia kuin läpimenon kasvattaminen.
Taulukkoon 1 on laskettu kolme skenaariota. Tarkasteltaessa taulukkoa havaitaan, että läpimenon kasvattamisella kasvutilanteessa on huomattavasti suurempi vaikutus tulokseen kuin kustannusrakenteen purkamisella. Mikäli sama taloudellinen vaikutus halutaan saada aikaiseksi, tulee resursseja purkaa merkittävästi enemmän suhteessa läpimenon kasvattamiseen.
Taulukko 1. Vertailu: läpimenon kasvattaminen vs. resurssien purkaminen.
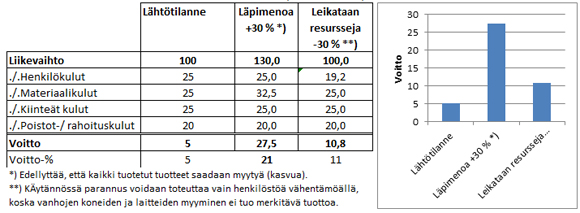
Virtauksen parantaminen
Toinen esimerkistä huomattava tekijä on läpimenon kannalta kokonaisläpimenoon vaikuttavan vaiheen tunnistaminen. Vaihe yksi on kokonaisuuden kannalta pullonkaula. Tämä voi toki vaihtaa paikkaa, jos raa’assa prosessiajassa on suurta vaihtelua. Jos kuitenkin oletetaan, että pullonkaula on vaihe yksi, tulee arvon tuottamisen suhteen parannustoimenpiteet kohdistaa vaiheeseen yksi. Toimenpiteet vaiheeseen kaksi ei kasvata virtausta vaan alkaa itse asiassa tässä tapauksessa ”vaatimaan” enemmän työtä vaiheelta yksi. Jos asiaa ei yrityksessä tai organisaatiossa havaita, kuormittuu vaihe yksi entisestään lisää.
Leanissa hukka täytyy sitoa aina arvon tuottamiseen ja läpimenoon. Muissa tapauksissa yrityksessä tai organisaatiossa voidaan ajautua tilanteeseen, jossa hukka vaihtaa vain paikkaa. Hyvä ymmärrys ei arvoa lisäävästä ajasta, sen syistä sekä sen aiheuttajiin tehtävistä muutoksista on kriittinen osa Leania.
Muda, Mura ja Muri
Hukka (waste) käsite on luotu ei arvoa lisäävän ajan rinnalle. Hukka voidaan jakaa karkeasti kolmeen luokkaan Muda, Mura ja Muri/6/.
Muda (waste) on ehkä yleisimmin tunnettu ja käytetty hukan muoto ”lean-yrityksissä” ja koulutuksissa. Hukan luokat ovat: ylituotanto, varasto, kuljetus, liike, yliprosessointi, odotus ja laatuongelmat tai uudelleen tekeminen. Tämä tunnetaan seitsemänä hukan muotona. Myöhemmin tähän joukkoon on tullut mukaan vielä kahdeksas hukka: osaamisen vajaa käyttö (tosin tämä poikkeaa muista seitsemästä merkittävästi). Hukan muodoista on havaittavissa, että kaikki voidaan havaita tai selvittää toiminnasta ja ne käsittelevät toiminnassa esiintyvää ei toivottavaa tilannetta. Nämä ovat oireita, ei syitä.
Mura on epätasapaino (unbalanced), joka havaitaan missä tahansa toiminnassa. Tämä ei ole ainoastaan linjan epätasapaino vaan mikä tahansa toiminta tai työsuoritus joka ei tapahdu tasapainossa. Tämäkin hukan muoto on ilmiö joka havaitaan toiminnoissa. Tämäkin on oire, ei syy. Systeemissä on aina vaihtelua, josta seuraa että tasapainoa mahdoton saavuttaa. Tämä auttaa paljastamaan läpimenon esteen eli pullonkaulan. Kysynnän ja ominaispiirteen muodostumisajan vaihtelusta johtuen systeemin alkaa kertyä hukkaa, nostaa tämä esiin systeemissä olevat ongelmat.
Muri on ylikuormitus (overburning) joka kohdistuu työsuorituksen tekevään kohteeseen. Tämäkään ei ole käsittele vain konetta, linjaa tai tehdasta vaan mitä tahansa toimintoa missä tapahtuu arvon lisäystä. Tämäkin hukan muoto on oire, eikä syy. Koska kysyntä ja ominaispiirteen muodostumisaika aina vaihtelee, vaikeutuu kuormituksen suunnittelu. Ylikuormitus paljastaa kuormitusongelman.
Usein hukan muodot Mura ja Muri on sivuutettu ja keskitytty vaan Mudaan. Tälle voisi hakea selitystä että se on helposti ymmärrettävissä ja se ”lyö läpi” missä tahansa, jos asiaa ei tarkastele kriittisesti. Womack toteaa eräässä kirjoituksessa, että hän esitteli Mudan ensimmäisenä ja nosti sen esiin, koska se oli helppo kertoa ja kuulijat ymmärsivät sen helposti. Tämä ei kuitenkaan tarkoita, että Muda olisi jotenkin tärkeämpi kuin nämä muut hukan muodot. Kaksi muuta ovat vähintään yhtä tärkeitä (Womack: Muri, Mura, Muda?).
Hukan määrittelyistä huomataan, että hukka on aina seuraus jostakin. Hukkien tunnistaminen on itse asiassa keino nostaa ongelmat esiin. Hukan tunnistaminen kertoo, että toiminnassa on ongelmia. Hukka on seurausta huonosta vaihtelun hallinnasta. Jos vaihtelua ei olisi, ei olisi ongelmia tehdä päätöksiä tulevista tapahtumista ja ”kaikki” onnistuisi. Tästä aiheesta Eero E. Karjalainen julkaisi 5.2.2014 artikkelin: Käytätkö oikeaa parannusmenetelmää.
Ongelmat voidaan luokitella neljään luokkaan jotka on esitelty kuvassa 4.
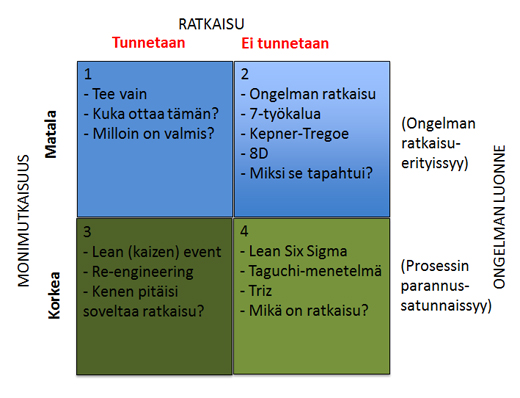
- Ongelmanratkaisu on ennalta tunnettu, aiheyhteys on yksinkertainen
- Ongelmanratkaisu on ennalta tunnettu, aiheyhteys on monimutkainen
- Ongelmanratkaisu ei ole ennalta tunnettu, aiheyhteys on yksinkertainen ja epästabiilisuusongelma(erityissyyvaihtelu)
- Ongelmanratkaisu ei ole ennaltatunnettu, aiheyhteys on monimutkainen jasuorituskykyongelma (satunnaisyyvaihtelu)
Onpa ratkaisu tunnettu tai ei, tämä ei tarkoita, että ratkaisu olisi helppo toteuttaa.
Lopuksi
Lean on arvon lisäämisen ja läpimenon kiihdytystekniikka. Hukka (Muda, Muri tai Muda) on keino epäkohtien havaitsemiseen. Taustalla voi olla ongelma, johon on tunnettu tai ei tunnettu ratkaisu. Ratkaisun löytyminen voi olla helppoa tai vaikeaa. Liiketoiminnan kannalta hukkaa kuitenkin tulee poistaa sieltä, missä kokonaisuutta tarkastelemalla se estää arvon muodostumista tai läpimenon kasvattamista. Hukan poistaminen ei automaattisesti tarkoita parempaa tulosta. Toimintaa ohjaavien lakien sekä systeemin ymmärtäminen kokonaisuutena ja vaihtelun merkitys tulee ymmärtää tuloksellisen kehitystoiminnan aikaan saamiseksi.
Lähteet:
1. Womack, J. & Jones, D. 2003. Lean Thinking – Banish Wasre And Create Wealth in Your Corporation. Free Press
2. George, L. M. 2002. Lean Six Sigma Combining Six Sigma Quality with Lean Speed. McGraw-Hill. USA.
3. Hopp, W. J. & Spearman, M. L. 2008. Factory Physics third edition. McGraw-Hill Irwin.
4. Georgantzas, N. C. & Katsamakas, E. 2008. Tampering dynamics: SD-SPC insight. Human Systems Management 27. 2008. p.89-108.
5. Hoerl, R. & Snee, R.D. 2002. Statistical Thinking – Improving Business Performance. Wiley & SAS Business. New Jersey.
6. Pascal, D. 2007. Lean Production Simplified. Shingo Price.
7. Roger W. Hoerl ja Ronald D. Snee: One Size Does Not Fit All – Identifying the right improvement metodology, Quality Progress, May 2013
Tilaa uutiskirje
Liity postituslistalle ja saat uusimmat artikkelit suoraan sähköpostiisi.
Tämä lomake on suojattu Google reCAPTCHA:lla. Lue tietosuojaseloste ja käyttöehdot.
Liittymällä postituslistalle hyväksyt Quality Knowhow Karjalainen Oy:n tietosuojaselosteen ja Quality Knowhow Karjalainen Oy voi lähettää sinulle ajankohtaisia artikkeleita, videoita sekä tietoa ja tarjouksia kursseista, kirjoista sekä ohjelmistoista.
Tämä lomake on suojattu Google reCAPTCHA:lla. Lue tietosuojaseloste ja käyttöehdot.