Uskomatonta, että kukaan maailmassa ei ole oppinut soveltamaan Toyotalla opittuja menetelmiä yhtä hyvin kuin Toyota. Toyotan tuotantosysteemin ydin perustuu useiden lähteiden mukaan imuohjauksesta, paikan päälle menemisestä, toisen kunnioittamisesta ja nopeista 5 kertaa miksi analyyseistä. Tämä kaikki on yhdistetty Demingin popularisoimaan PDSA-ympyrään. Voiko tämä olla totta?
Menetelmät, jotka kirjoissa esitellään, ovat joko 1900-luvun taitteesta tai 1950–1970-luvuilta. Onko näin, että Toyotalla ei käytetä tuotannon tai palvelujen kehittämiseen uudempia tekniikoita, statistiikkaa, tietokoneiden laskutehoa jne…? Allekirjoittanut ainakin epäilee.
Perehtymällä Toyotan tuotantosysteemiin syvällisemmin ja tutkimalla taustaa saa erilaisen kuvan menetelmästä. Useissa kohdissa annetaan ymmärtää, mutta ei suoraan sanota, että tarvitaan erityisosaamista. Kun puhutaan stabiilisuudesta, huomaa epäsuoria viittauksia tilastollisen prosessin ohjaus (SPC) konseptiin. On selvää, että organisaatio tarvitsee asiantuntijoita. Ongelma vain on, että missään ei mainita, mikä on asiantuntijoiden osaamisvaatimus (BOK – Body Of Knowledge). Pääpaino kirjoissa on osallistumisessa ja kulttuurissa sekä tietysti visualisoinnissa (sehän on se, mikä tehtaalla näkyy). Toisaalta tiedetään, että W.E. Deming, J.M. Juran, G. Taguchi ovat kouluttaneet puheidensa perusteella vuosia japanilaisia asiantuntijoita ja johtajia. Näistä herroista tiedetään se, että he vannoivat systeemiajattelun, vaihtelun, tietotaidon ja psykologian perään. Ei siis ainoastaan psykologian.
Edistyksellisten menetelmien ja asiantuntijoiden roolista löytyy yksi selvimmistä todisteista 1990 Kenichi Sekinen kirjoittamasta kirjasta One-Piece-Flow. Kirjan esimerkissä asiantuntijat lyhentävät 800 tonnisen muovipuristuskoneen värin ja muotin vaihtoaikaa noin 95 minuutista alle 6 minuuttiin. Esimerkissä käytetään ideoiden testaamiseen Taguchin L8-matriisia testauksessa (kuva 1). Esimerkissä on taitavasti yhdistetty PDSA-ympyrä, ryhmätyö, osaaminen, prosessissa työskentelevät henkilöt ja edistykselliset laatutekniikan työkalut.
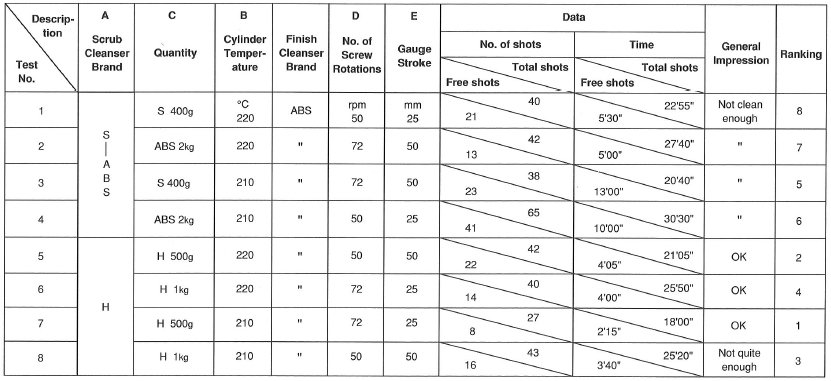
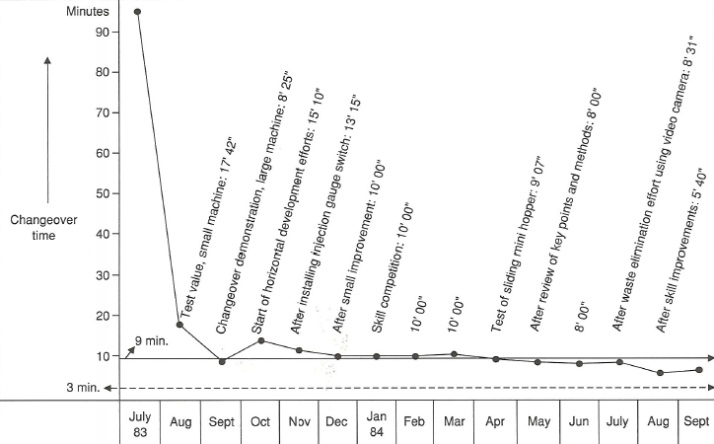
Usein kirjallisuudessa painotetaan kaikkien osallistumista ja mukana oloa, joukkovoimaa. Tämä on oikein, mutta ei voi unohtaa tietotaidon, tieteen ja teorian arvoa teollisen yhteiskunnan tuottavuuden kasvussa. Ei voi olla mahdollista, että pelkällä joukkovoimalla teollisen ajan aikana tuottavuutta on voitu nostaa liki satakertaisesti sadassa vuodessa.
Vuonna 2004 professori Konichi Shimizu julkaisi tutkimuksen Toyotan jatkuvasta parannuksesta. Hän jakoi parannukset kahteen luokkaan sen perusteella, mikä ryhmä parannukset teki. 10 prosenttia parannustuloksista tulee hänen mukaansa henkilökunnalta ja 90 prosenttia on peräisin asiantuntijoiden tekemisestä. Asiantuntijoiden vastuulla on tuottavuuden kehittäminen, kun taas henkilökunnan rooli on nostaa ongelmat esiin ja osallistua laatupiiritoimintaan (Kaizen), jotta nähdään keistä on tekemään jatkossa parannuksia. Tätä tutkimusta tukee myös kysymys, kuinka monella työntekijällä on oikeus muuttaa systeemejä? Yleensä vain johdolla, tai heidän valtuuttamilla henkilöillä on oikeus tehdä radikaaleja muutoksia.
Maailman laatupäivillä Helsingissä 10.11.2011 Hoerl puhui GE:n menestystekijöitä Lean Six Sigman toteutuksessa. Hän listasi viisi tekijää, josta kaksi liittyi osaamiseen. Ensimmäisenä tekijänä oli riittävä osaaminen toteuttajilla ja toisena tekijänä asiantunteva koulutus ja tuki asiantuntijoille. kolme muuta olivat Johdon sitoutuminen ja vastuu sitoa kehityskohteet strategisiin päämääriin. Neljäs asia oli prosessi- ja systeeminäkökulma toimintaan ja viides käsitteli riittävää resursointia, lähinnä aikaa, toteuttajille.
Tuottavuus ja tehostusihmisten piirissä vallitsee käsitys, että Lean, TPM (Total Productive Maintenance), TPS jne… toteutetaan vierailemalla yrityksissä, oppimalla toisilta ja katselemalla. Professori Ingnisio toteaa, että jos 1700-luvulla tätä keinoa yritettiin, mutta epäonnistuttiin täysin. Venetsiassa oli ensimmäiset ”kokoonpanolinjat”, joissa valmistettiin sotalaivoja 1-3 kappaleen päivä vauhdilla. Hänen sanojen mukaan käynnistyi teollisuusturismin aika. Mentiin paikan päälle ja kotiin tullessa kopioitiin, mitä nähtiin. Kun olisi pitänyt ymmärtää mitä ei nähty, ja soveltaa näkemäänsä tämän jälkeen, jos enää on tarvetta. Vierailu on toki tärkeää. Yhtä tärkeää kuinka verkostoituminen, mutta sisältö vain turhan kevyt ja luullaan oppivan jotain suurta, eikä itse huomata saadun tiedon keveyttä ja käyttömahdottomuutta.
Juuri ilmestyneessä The Lean Handbook -kirjassa on kuvattu mitä Lean -ammattilaisen tulee hallita. Kirja pitää ensimmäistä kertaa sisällään Body of Knowledgen. Kirja sisältää kuvauksen konsepteista ja työkaluista mitä tarvitaan asiakkaan tarpeen määrittämisestä, tuotteen ja prosessin suunnitteluun ja parantamiseen. Deming korosti aihepiiritiedon (substanssitieto) ja syvällisen tiedon (kuinka luodaan uutta tietoa) merkitystä. Ihmisten osaaminen ja erilaisen teknologian (konseptit ja työkalut) yhdistämisestä syntyy uutta tietoa, jotka voidaan käyttää toiminnan parantamisessa.
Edellä kirjoitetulla ei luonnollisesti tarkoiteta, että henkilökunnan panos ei olisi merkittävä vaan päinvastoin. Yleensä muutokset koskevat heitä, heidän toimintatapojaan, joten heidän halua osallistua ja muuttaa toimintatapojaan, on kriittinen tekijä parannuskulttuurissa. Johdon tehtävä on balansoida osallistumisen ja osaamisen keskittämisen kanssa. On selvää, että tarvitaan uutta tietotaitoa, johtamista ja osallistumista, jos halutaan menestyä nyt tai tulevaisuudessa.
Mitä enemmän Leaniin perehtyy, päätyy opetukseen: hanki riittävä tieto ja taito Leanista, jos aiot menestyä Lean-parannuksissa.
Lähteet:
- Hoerl, R.W. 10.11.2011. Luentoaineisto: World Quality Day. Helsinki
- Ingnisio, J.P. 2009. Optimizing Factor Performance – Cost.Effective Ways to Achieve Significant and Sustaunable Improvement. McGraw Hill
- Manos, A. & Vincent, C. The Lean Handbook a Guide To the Bronze Certificatyion Body of Knowledge. ASq Quality Press. Milwaukee, Wisconsin
- Rother, M. 2010 Toyota Kata – Managing people for improvement, adaptiveness, and superior results. McGraw Hill
- Sekine, K. 1990. One-Piece Flow – Cell Design for Transforming the Production Process. Productivity
Tilaa uutiskirje
Liity postituslistalle ja saat uusimmat artikkelit suoraan sähköpostiisi.
Tämä lomake on suojattu Google reCAPTCHA:lla. Lue tietosuojaseloste ja käyttöehdot.
Liittymällä postituslistalle hyväksyt Quality Knowhow Karjalainen Oy:n tietosuojaselosteen ja Quality Knowhow Karjalainen Oy voi lähettää sinulle ajankohtaisia artikkeleita, videoita sekä tietoa ja tarjouksia kursseista, kirjoista sekä ohjelmistoista.
Tämä lomake on suojattu Google reCAPTCHA:lla. Lue tietosuojaseloste ja käyttöehdot.